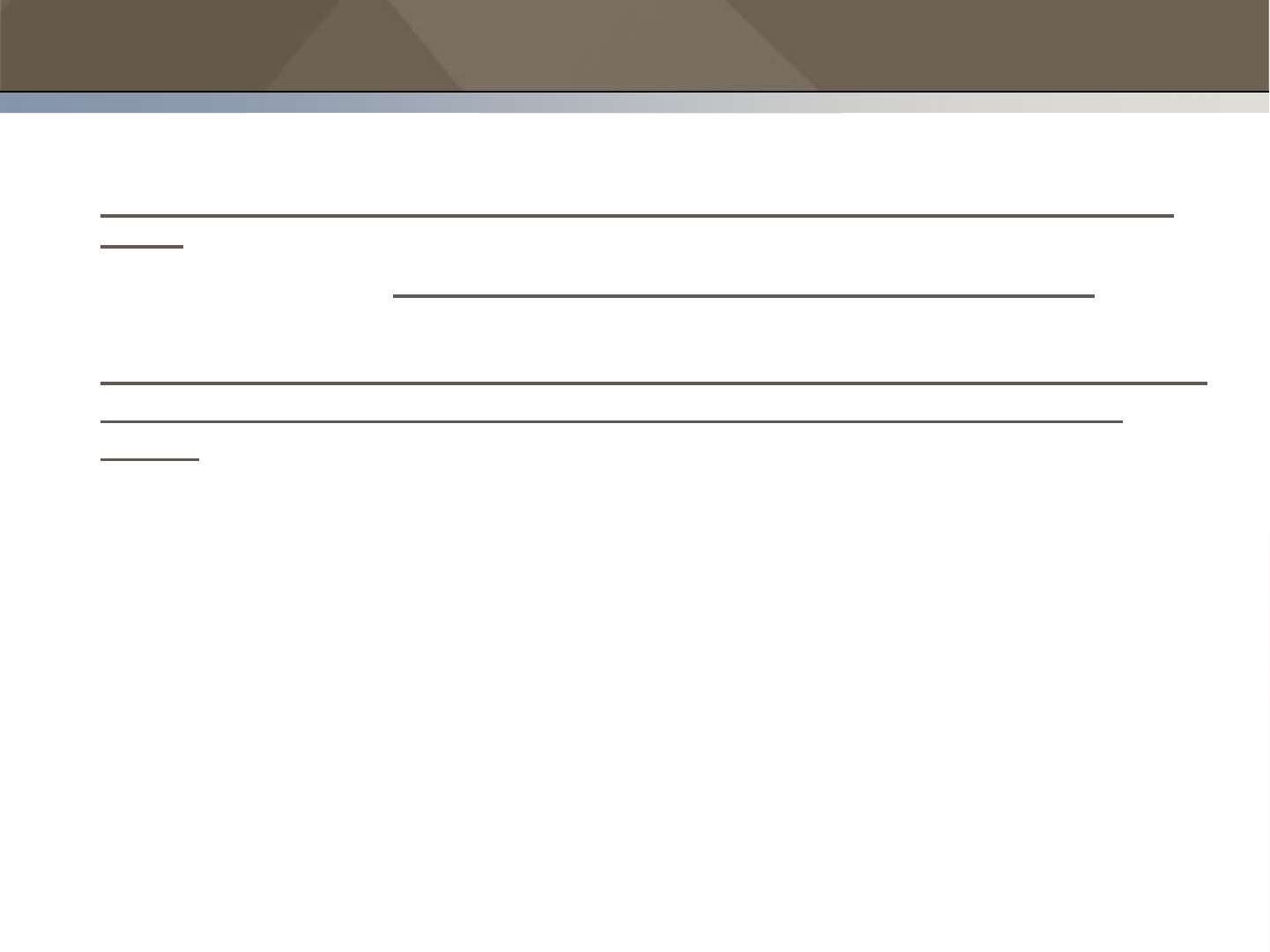
ReferencesReferences
Works Cited
• ISO 11607, Packaging for Terminally Sterilized Medical Devices, Parts 1
and 2. 2006th ed. AAMI, 2006.
• "Medical Devices." U S Food and Drug Administration Home Page. 07
June 2009 <http://www.fda.gov/MedicalDevices/default.htm>.
• ISO/TS 16775:2014, Guidance on the application of ANSI/AAMI/ISO 11607,
Packaging for Terminally Sterilized Medical Devices, Part 1 and Part
2:2006.
• Statistical Reference: Determining Sample Size by Glenn D. Israel,
University of Florida IFAS Extension, PE0D6, published 1992 and
reviewed 2009 and Cliffs Quick Review Statistics by David H. Voelker,
Peter Orton and Scott V. Adams, Wiley Publishing, Inc. 2001, page 79.
• Juran’s Quality Handbook, fifth edition, by Joseph M. Juran, A. Blanton
Godfrey, 1998, page AAII.36.