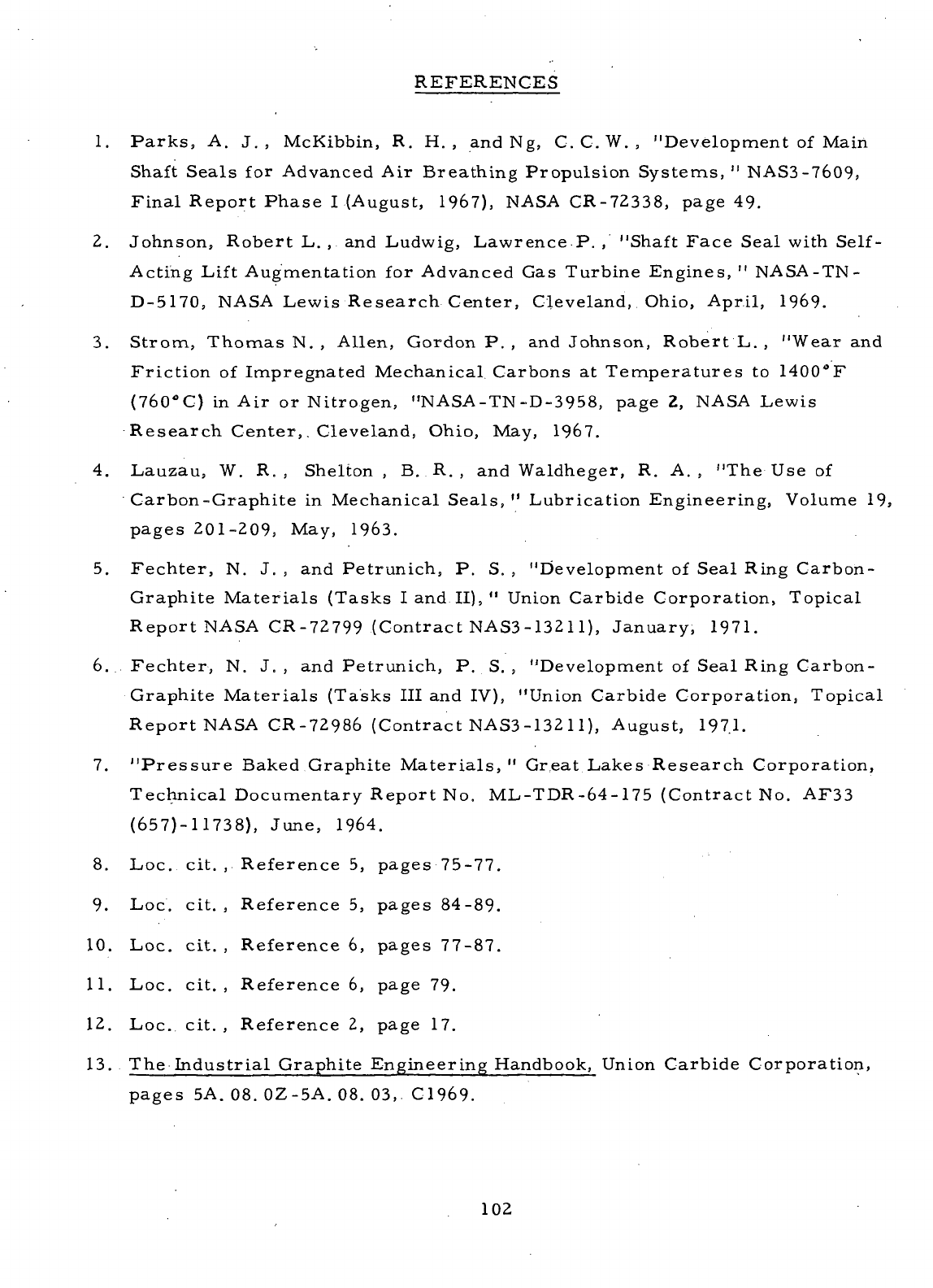
REFERENCES
1.
Parks,
A. J. ,
McKibbin,
R. H. , and Ng, C. C. W. ,
"Development
of
Main
Shaft
Seals
for
Advanced
Air
Breathing Propulsion Systems,
"
NAS3-7609,
Final
Report
Phase
I
(August,
1967),
NASA
CR-72338,
page
49.
2.
Johnson, Robert
L. , and
Ludwig, Lawrence
P. ,
"Shaft
Face
Seal
with Self-
Acting
Lift
Augmentation
for
Advanced
Gas
Turbine Engines,
"
NASA-TN-
D-5170,
NASA
Lewis Research Center, Cleveland, Ohio, April, 1969.
3.
Strom,
Thomas
N. ,
Allen, Gordon
P. , and
Johnson, Robert
L. ,
"Wear
and
Friction
of
Impregnated Mechanical Carbons
at
Temperatures
to
1400°F
(760°C)
in Air or
Nitrogen, "NASA-TN -D-3958, page
2,
NASA
Lewis
Research
Center,, Cleveland, Ohio, May, 1967.
4.
Lauzau,
W. R. ,
Shelton
, B. R. , and
Waldheger,
R. A.,
"The
Use of
Carbon-Graphite
in
Mechanical
Seals,"
Lubrication Engineering, Volume
19,
pages 201-209, May, 1963.
5.
Fechter,
N. J. , and
Petrunich,
P. S. ,
"Development
of
Seal
Ring Carbon-
Graphite
Materials
(Tasks
I and
II),
"
Union
Carbide Corporation, Topical
Report
NASA
CR-72799
(Contract
NAS3-13211),
January, 1971.
6.
Fechter,
N. J. , and
Petrunich,
P. S. ,
"Development
of
Seal
Ring Carbon-
Graphite
Materials
(Tasks
III and
IV), "Union Carbide Corporation, Topical
Report
NASA
CR-72986
(Contract
NAS3-13211),
August,
197.1.
7.
"Pressure
Baked Graphite
Materials,"
Great
Lakes
Research Corporation,
Technical
Documentary Report
No.
ML-TDR-64-175 (Contract
No.
AF33
(657)-11738),
June, 1964.
8.
Loc. cit.
,
Reference
5,
pages 75-77.
9.
Loc. cit., Reference
5,
pages
84-89.
10.
Loc. cit.
,
Reference
6,
pages 77-87.
11.
Loc. cit., Reference
6,
page
79.
12.
Loc. cit., Reference
2,
page
17.
13. The
Industrial Graphite Engineering Handbook,
Union
Carbide Corporation,
pages
5A. 08.
OZ-5A.
08.
03,.
C1969.
102